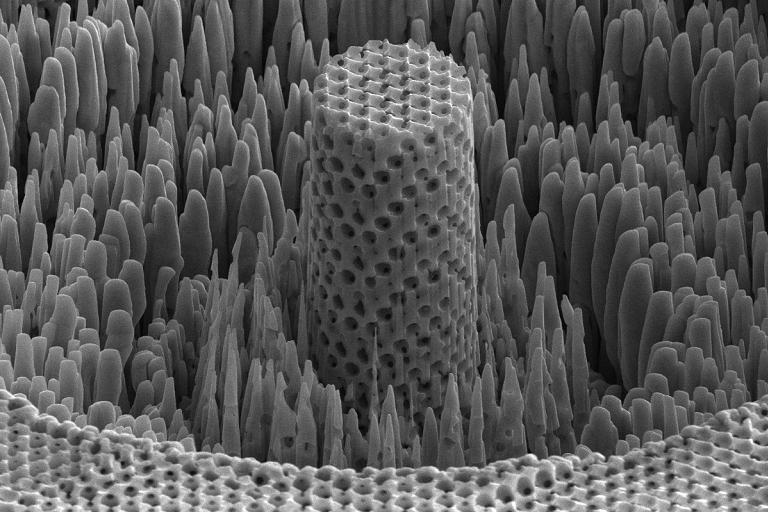
Sim, já existe uma madeira mais dura que o aço e o titânio, mas James Pikul, da Universidade da Pensilvânia, nos EUA, queria inverter a equação.
Assim, ao invés de fabricar uma madeira que se parece com metal, ele fabricou um metal que se parece com madeira.
O resultado é igualmente promissor em termos de versatilidade e de aplicações práticas: uma folha de níquel com poros em nanoescala que tornam o material tão forte quanto o titânio, mas de quatro a cinco vezes mais leve.
Embora seja largamente usado na indústria aeroespacial e em materiais esportivos, as propriedades do titânio dependem da maneira como os átomos do metal são empilhados. Na prática, defeitos aleatórios que surgem no processo de fabricação significam que o metal atinge apenas uma fração da força que poderia teoricamente ter – o titânio é tão forte quanto o aço, mas cerca de duas vezes mais leve.
Trabalhando na escala dos átomos individuais, portanto, é possível construir novos materiais com proporções de força-peso ainda melhores. Um bloco de titânio no qual cada átomo estivesse perfeitamente alinhado com seus vizinhos seria dez vezes mais forte do que o que pode ser produzido atualmente.
Metal celular
Foi nisso que Pikul se inspirou, projetando estruturas porosas em nanoescala. O espaço vazio dos poros e o processo de automontagem com que são feitos tornam o metal poroso semelhante a um material natural – a madeira – e ganhe muito em força e leveza.
“A razão pela qual chamamos [este material] de madeira metálica não é apenas sua densidade, que é mais ou menos a mesma da madeira, mas sua natureza celular,” detalha Pikul. “Os materiais celulares são porosos; se você olhar para os grânulos da madeira, você verá partes que são grossas e densas e feitas para sustentar a estrutura, e partes que são porosas e feitas para suportar funções biológicas, como o transporte entre as células.”
A madeira metálica tem essa mesma estrutura, com áreas grossas e densas, com barras metálicas resistentes, e áreas porosas com lacunas de ar. As barras de suporte têm apenas 10 nanômetros de largura, o que equivale a cerca de 100 átomos de níquel, algo que não se pode ainda obter com impressoras 3D, por exemplo, que tipicamente imprimem com resolução na faixa das centenas de nanômetros.
Outra grande vantagem é que a madeira metálica se compara ao titânio, mas é feita de níquel, um metal bem mais barato.
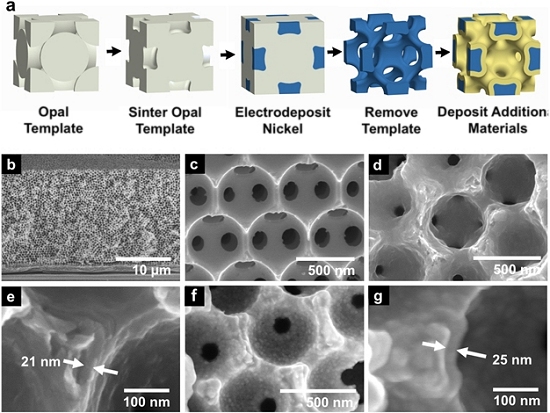
Fabricação da madeira metálica
O método desenvolvido por Pikul começa com minúsculas esferas de plástico, com algumas centenas de nanômetros de diâmetro, suspensas em água. Quando a água é lentamente evaporada, as esferas se assentam e ficam empilhadas como laranjas em uma caixa, fornecendo uma estrutura ordenada e cristalina.
Usando galvanoplastia, a mesma técnica que adiciona uma fina camada de cromo a peças de carros, as esferas de plástico recebem uma infiltração com níquel. Uma vez que o níquel se assenta entre os poros, as esferas de plástico são dissolvidas com um solvente, deixando uma rede aberta de suportes metálicos.
Como aproximadamente 70% do material resultante é espaço vazio, a densidade dessa madeira metálica feita de níquel é extremamente baixa em relação à sua resistência – com uma densidade igual à da água, um bloco de madeira metálica flutua da mesma forma que um bloco de madeira vegetal.
A equipe agora pretende escalonar sua técnica para a produção em larga escala, fornecendo uma alternativa mais barata, mais leve e mais forte do que o titânio metálico.
High strength metallic wood from nanostructured nickel inverse opal materials
James H. Pikul, Sezer Özerinç, Burigede Liu, Runyu Zhang, Paul V. Braun, Vikram S. Deshpande, William P. King
Nature Scientific Reports
Vol.: 9, Article number: 719
DOI: 10.1038/s41598-018-36901-3
Fonte: Site Inovação Tecnologica